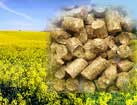
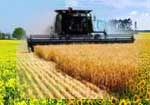
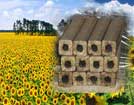
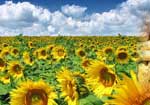
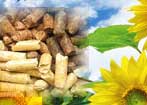
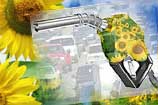
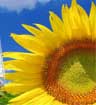
2. Pellets 8mm
3. 6-8 mm DIN+ Quality Pellets
4. We manufacture and sell fuel pellets from straw to European countries
5. Sell wood pellets
6. Wood pellet manufacturing
7. Sunflower Husk Pellets
8. Din Plus Wood Pellets
9. Export of sunflower husk pellets to the European market
10. Export of sunflower husk pellets to the European market
The effect of regime parameters on pressing efficiency and quality of wood pellets
Sun-14-2018
Moisture content of Biomass
The moisture present in the biomass facilitates starch gelatinization, denaturation of the protein, and solubilization of the fibers during the granulation process. Biomass treated with steam has better properties, since additional thermal energy changes the physicochemical properties to such an extent that the bond between the particles is significantly increased. This leads to improved pelletizing quality. S. Mani with co-authors notes that moisture in biomass during the pelleting process acts as a binder and increases adhesion with the help of van der Waals forces, thereby increasing the contact area between the particles. A. Demirbas found that an increase in the moisture content in spruce sawdust from 7 to 15% significantly increases the strength of the granules. O.D. Müller found that in the humidity range of 8.5 to 15%, wood pellets made from aspen have a high mechanical strength http://eufuel.de/news-operating-condition-in-pressing-efficiency-and-woo-5.html.
Many researchers came to the conclusion that the optimum moisture content for pelletizing biomass differs for each individual raw material and processing conditions. Thus, the optimal moisture content for compaction of beech was from 6 to 10%, for spruce about 10%, for pine from 6 to 8%, for aspen 10-12% for olive cellulose 5%. Many scientists emphasize that increasing the moisture content of raw materials above the optimum can have a negative effect on the mechanical properties and density of pellets. In addition to the quality of the compacted raw materials, the granulation process itself depends on the moisture content. D. Andreiko and J. Grochowicz found that energy costs for pressing decrease with increasing moisture content from 9.5% to 15.0%. P. Rousset and co-authors have shown that an increase in the moisture content of pine and beech raw materials reduces the need in energy for pelletizing.
Particle size, shape and location of biomass
Before pelletizing, the biomass is ground to a certain particle size. J.D. Payne argues that a certain percentage of fine particles is required to improve granulation efficiency and reduce costs. J.B. Dobie has proved that finely grinding raw materials allows to obtain pellets with a higher density, increases the productivity of the granulator, since the material passes through the matrix more easily. There is a critical particle size below which granulation is not advisable because too small particles can stick the granulator. P.D. Jensen, M. Temmerman and S. Westborg in the research of the particle size effect on the quality of pellets have revealed that a high particle content of less than 0.5 mm in diameter has a negative effect on friction and results in a decrease in pellet quality. They note that the content of fine particles should not exceed 10 to 20%, unless a binder is added. O.D. Müller notes that granules obtained by grinding a raw material with a hammer mill using a sieve with a hole diameter of 0.8 mm have reduced quality features.
Source: http://ukrfuel.com/news-regime-parameters-wood-pellets-140.html
Any copying and distributing withoutactive hyperlink is strictly prohibited!
Views: 2332
Stobart biomass division is to make a deal
Biomass Related News
- New revolutionary research in solar energy
- Solar power battery charging becomes reality
- Chemical properties of charcoal
- Facilities of the municipality of Kiihtelysvaara, Finland heated by wood pellets
- Drax begins new health promotion sessions
- Breakthrough in efficiency of solar panel
- 150-Year-Old Galapagos tortoise Dies at San Diego Zoo
- Ikea invests in renewable energy in UK selling solar panel
- Spanish renewable energy firm wants to sell plants
- Wood pellets production cost
© Ukrainian Biofuel Suppliers 2008-2024 |