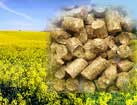
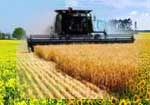
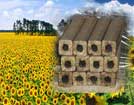
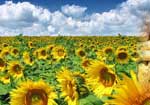
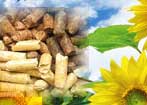
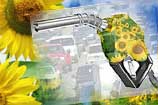
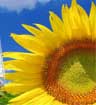
2. Pellets 8mm
3. 6-8 mm DIN+ Quality Pellets
4. We manufacture and sell fuel pellets from straw to European countries
5. Sell wood pellets
6. Wood pellet manufacturing
7. Sunflower Husk Pellets
8. Din Plus Wood Pellets
9. Export of sunflower husk pellets to the European market
10. Export of sunflower husk pellets to the European market
The multipurpose bioenergy plant in Skelleftea, Sweden
Tue-15-2011Skelleftea Kraft is a municipally-owned company in the north-east of Sweden. In and around Skelleftea, the company owns a large and growing network of district-heating pipes serving local households and businesses. Skelleftea Kraft also owns and operates power stations running on hydro-power and nuclear power, and heat-and-power plants fuelled with biomass. This chapter will describe the largest of those biomass plants, located at Hedensbyn in Skelleftea, which (at full power) produces 35,6 MWe, and 62,9 MWth for the district heating and 29 tonnes/h of biopellets.
Skelleftea CHP plant
Skelleftea Kraft has two CHP plants using wood fuel and a number of different heating plants using wood, peat and oil as fuel. Skelleftea CHP plant 1 is fuelled with biomass-residues, amounting to about 200,000 wet-tonnes (450 GWh) a year, which consist mainly of sawdust, but also of bark, peat, and the branches and tops of trees that are trimmed off when they are felled. The CHP plant, which cost around SEK 310 million (ECU 34 million) to build, was ordered in May 1994 and test operation started at the end of 1996. It has an output of approximately 63 MW of heat and 35 MW of electricity.
The CFB Pyroflow compact boiler was supplied by Foster Wheeler, and is fuelled with unprocessed biofuel, such as wood chips and bark. Steam is produced at a pressure of 140 bar(a) and a temperature of 540°C to the steam turbine, which was supplied by ABB Stal.
The steam turbine is of the VAX type and consists of two modules: a high pressure one and a low-pressure one, with a two-stage district heating exhaust. By using two turbine modules, it is possible to run them at different speeds to maximise efficiency. The HP module runs at 10700 r/min and the LP module at 6950 r/min. The modules drive a common generator in a single-string arrangement. When the plant was planned, the turbine was designed with extraction of steam up to 9 kg/s and 26 bar. That enabled the process steam to be used for drying biofuel.
Pellet plant
The pellet manufacturing plant was ordered in June 1996. The order included biofuel handling system, steam dryer, steam recovery system, low pressure turbine, cooling water system, pelletisation and ship loading facilities with storage at a cost of SEK 216 million (ECU 24 million) The test operation started in May 1997.
The raw material for the pellets production consists of sawdust from sawmills. The incoming biofuel amounts to around 56 ton/h with a moisture content of about 55 %. The sawdust is sieved before it is fed into the steam dryer at 4.5 bar. The dryer consists of two 1.6 m wide and 30 m high vertical condensers, with 121 tubes, each diameter is 110 mm. The fuel is transported through the tubes by a large fan and stays in the drying zone for about 30 seconds to reduce the moisture content to 9 %, before the fuel is fed to the pellet mills. The drying steam (270°C and 26 bar) from the CHP plant condenses outside the tubes and therefore does not mix with the steam which is produced from the wet fuel. The pure condensate from the dryer can in this way be used again.
When planning the integration of the pellet manufacturing process with the CHP plant, greal emphasis was placed on the efficient use of energy and the possibility to use this energy tc produce more electricity. For that reason we decided to install a process for recovering steam from the biofuel dryer in the pellet plant.
After the sawdust leaves the dryer, the fuel is treated and then ground in a milling line to make a coarse powder with a maximum particle size of 3 mm. After this, the powder is turned into 8 mm pellets using four parallel machines, and the pellets are cooled by air.
Electrical consumption in the pellet factory is around 100 kWh per tonne of pellets produced Even at full production, however, the pellet plant is more than self-sufficient in electricity because of the recovery process described.
Pellet production can reach around 30 t/h when the plant is operating at full capacity. The production level can be varied according to the demand for district heat - and consequently the supply of steam - as well as the demand for pellets. Annual production is expected to be arounc 130,000 tonnes. This should be seen as part of the total energy output of the integrated CHP and pellet plant. Table 1 compares the total output of the integrated facility with that of the CHP plant alone.
The bulk of the pellets produced by SkellefteS Kraft is sold to existing heat water plants as a substitute for coal in their boilers. Due to their higher calorific value, as well as their even particle size and distribution of moisture content, pellets represent a much better replacement for coal than unprocessed biofuel.
Large proportion of the pelletized biofuel will be transported to customers by ship. In the nearby port of Skelleftehamn, a pellet store with a capacity of 45,000 m3 has been built, and a 900 t/h ship loading facility has also been installed.
Skelleftea Kraft also builds small district heating systems with pellet-fuelled boilers and converts small oil boilers to pellets for heating of houses and schools which are not connected to a district heating system. Although there is great potential for developing the demand for pellets in the domestic sector, it remains largely untapped. However, for household heating, there are already pellet burning units on the market, and stoves for pellet firing are also available. Compared with wood, pellets are much easier for the consumer to store and handle.
Source: http://ukrfuel.com/news-the-multipurpose-bioenergy-plant-in-skel-5.html
Any copying and distributing withoutactive hyperlink is strictly prohibited!
Views: 2554
Stobart biomass division is to make a deal
Biomass Related News
- How to make coconut shell charcoal
- Chemical properties of charcoal
- Wood pellet boiler prices: general overview
- 4 US ethanol plants are to be sold by Abengoa Bioenergy
- Providing renewal security to Drax Power Station
- Ikea invests in renewable energy in UK selling solar panel
- White Dog Labs has new innovative fermentation technology
- Burning wood biomass: an opportunity or a problem?
- 150-Year-Old Galapagos tortoise Dies at San Diego Zoo
- The Valley (Pembrokeshire) Ltd is seeking full planning permission
© Ukrainian Biofuel Suppliers 2008-2024 |